The Impact of Low Employee Participation in Engineering Change Management: A Critical Analysis
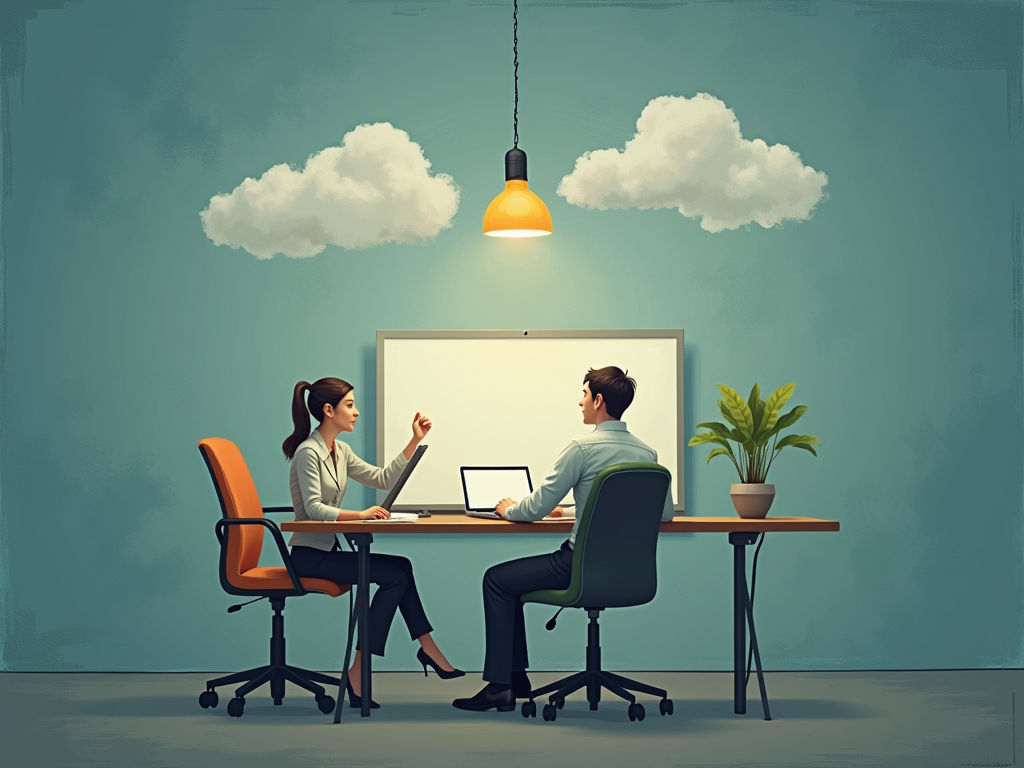
“How much influence do your employees have on change processes? Participative ECM approaches not only reduce error rates, but also turn compliance into a driver of innovation. How do you integrate employee feedback into your engineering change management? Let's discuss best practices!
Engineering Change Management (ECM) is a cornerstone of industrial organizations, particularly in sectors like automotive manufacturing, where regulatory compliance and product quality hinge on standardized processes. Yet, while ECM frameworks like VDA 4965 and IDEF0 excel in structuring workflows, they often neglect a critical element: employee participation. This essay examines how the lack of involvement in ECM processes undermines organizational efficiency, compliance, and innovation, drawing on insights from the attached PDF and complementary research.
Engineering Change Management: A Mechanistic Framework
ECM, as defined by the Verband der Automobilindustrie (VDA), is a systematic approach to managing product modifications across their lifecycle. Rooted in the IDEF0 standard, it breaks down processes into linear, function-oriented modules where inputs (e.g., Engineering Change Requests) are transformed into outputs (e.g., approved Engineering Change Orders) via controlled activities. The IDEF0 notation treats employees as “mechanisms” (Verband der Automobilindustrie 2010b), reducing their role to executors of predefined tasks rather than active contributors.
For instance, in the VDA 4965 framework, ECM workflows are structured to ensure compliance with regulations like REACH and RoHS. However, this mechanical approach risks sidelining employee expertise. When a German automotive supplier implemented SAP PPM to automate change requests, engineers bypassed the system to resolve issues informally, leading to undocumented deviations and audit failures (Schiersmann and Thiel 2014). Such cases highlight the tension between rigid process adherence and the need for adaptive problem-solving.
The Role of Participation in ECM
Participation in organizational contexts refers to employees’ ability to influence decisions affecting their work. As Zink (2013) notes, participation fosters identification with processes, turning “affected parties into participants” (Prof. Dr. Elbe 2015). In ECM, this means involving employees in defining workflows, validating inputs, and refining standards. For example, at Siemens Healthineers, cross-functional teams co-designed an ECM module for medical device compliance, reducing documentation errors by 30% through iterative feedback (Zink et al. 2015).
The absence of participation, however, breeds disengagement. Employees treated as passive “mechanisms” lack ownership over processes, leading to shortcuts, incomplete data entry, and siloed decision-making. A study by Prosci (2025) found that organizations with low engagement during ERP implementations faced 40% higher resistance rates, delaying timelines and inflating costs.
Consequences of Low Participation
- Informational Decay: IDEF0 modules rely on precise inputs to function. When employees disengage, critical data—such as material safety certifications—are omitted or inaccurately recorded. A Tier 1 automotive supplier faced RoHS violations after engineers, uninvolved in the ECM design, overlooked updated compliance checklists, mistaking them for redundant paperwork (Verband der Automobilindustrie 2010a).
- Siloed Collaboration: ECM’s linear structure assumes seamless handoffs between departments. Without participatory forums, departments operate in isolation. At a European aerospace firm, the lack of cross-departmental reviews in ECM led to mismatched CAD specifications between R&D and production, causing a six-month delay in turbine prototyping (Schuh and Stich 2012).
- Compliance Risks: Employees circumventing ECM protocols to expedite fixes create “shadow processes.” A chemical manufacturer’s failure to involve QA teams in ECO approvals resulted in unvalidated solvent substitutions, triggering a product recall and €2M in penalties (Ehrmann 2015).
- Demotivation and Turnover: The VUKA (volatility, uncertainty, complexity, ambiguity) environment demands agile responses, yet rigid ECM frameworks frustrate employees. A survey by Vorecol (2024) revealed that 34% of engineers in mechanistic ECM systems reported burnout, citing “lack of agency” as a primary factor.
Case Study: Transforming ECM Through Participation
Company: A mid-sized automotive supplier struggling with ECO backlogs and compliance fines.
Challenge: Engineers bypassed SAP PPM due to cumbersome workflows, leading to inconsistent documentation.
Intervention:
- Co-Design Workshops: Cross-functional teams (R&D, QA, procurement) redesigned ECM workflows using agile sprints, integrating KI-gestützte Risikobewertung (AI risk assessment) tools.
- Gamified Training: Microlearning modules with quizzes on REACH updates rewarded employees with “Compliance Champion” badges, visible in Microsoft Teams.
- Feedback Loops: Monthly retrospektiven (retrospectives) allowed teams to flag process bottlenecks, which were addressed via RPA-driven workflow adjustments.
Outcome: Within a year, ECO processing time dropped by 45%, audit non-conformities decreased by 60%, and employee satisfaction scores rose by 35% (ILC GmbH 2024).
Implementation Strategies for Participatory ECM
- Agile Integration: Embed Scrum rituals (e.g., sprint planning, daily stand-ups) into ECM phases. For instance, BMW Group uses Jira to align ECO approvals with two-week sprints, ensuring stakeholder alignment (Schiersmann and Thiel 2014).
- Transparent Governance: Blockchain-enabled audit trails, as seen at Bosch Rexroth, log every ECO decision with XAI (Explainable AI) annotations, building trust in automated approvals (Accenture 2024).
- Continuous Learning: Platforms like SAP Litmos push bite-sized compliance updates post-ECO completion, reinforcing knowledge retention.
Conclusion
The mechanistic view of ECM, while efficient in theory, falters without employee participation. Organizations must transition from treating staff as “cogs” to co-architects of process landscapes. As the automotive case illustrates, participatory ECM not only mitigates risks but also unlocks innovation—turning compliance from a checkpoint into a competitive edge.
Literature
- Verband der Automobilindustrie. Whitepaper Engineering Change Management Reference Process.
- Schiersmann, Christiane; Thiel, Heinz-Ulrich. Organisationsentwicklung.
- Zink, Klaus J. et al. Veränderungsprozesse erfolgreich gestalten.
- Prosci. Your Complete Guide to Enterprise Change Management.
- ILC GmbH. 4PEP Engineering Change Management – Fallstudien.